June 28, 2022
Our expertise is underground
The people who follow Normet may have noticed that we pride ourselves on being experts in our customers' underground production processes. Communicating this to our audience aims to let people know that we know the processes that we develop solutions for, but what does it mean for us?
Cyclic Process
Tunnel excavation is a cyclic process with pretty much all other methods than the Tunnel Boring Machine (TBM). In one way or another, excavating the material is followed by getting it out of the tunnel space, and supporting the profile to be safe and ready for the next round of material to be excavated. This not only means that all the sub-processes need to be carefully planned and optimised, but also that the dependencies and impacts between them need to be evaluated and understood to optimise the whole tunnelling or mining cycle.

Tunnel excavation is a cyclic process where all sub-processes affect each other
Chance for improvement under every rock
Let’s look at hard rock drill and blast, for example, and start our morning shift with blast hole drilling for a new round. It’s clear that the blaster would want to have those holes nicely and neatly where they should be, to be able to charge the round for optimal blasting results.
But how does this affect the following processes?
Careful drilling pattern design and accurate drilling enables for accurate charging with no extra explosives used to substitute for hole deviations. This results in reduced overbreaks, smooth surface finish, and narrow damage zone.
There will be less rock to muck out, as the overbreaks are smaller. This combined with controlled particle size will lead to shorter and more predictable mucking times with no interruptions and less risks.
Smooth surface finish and a minor damage zone will have a great effect on scaling. There are less loose rocks and uncertainties in the surrounding rock mass, and the scaling will become more systematic. Again, time will be saved, and the schedule becomes more predictable. What’s absolutely most important, scaling can be done more safely for both the scaler operator and everyone entering the space afterwards.
A controlled damage zone will reduce the need for rock bolting, and again make the work safer. Even if the rock bolting would be systematic as is often the case in civil engineering tunnels, the smooth surface will cut down time needed for bolt hole drilling and make the work easier and safer as the holes stay clean and open.
As we know, concrete spraying is a highly material intensive process. A major part of the costs of sprayed concrete are in the concrete mix itself, and pretty much all the rest are dependent on concrete consumption. Also, unfortunately the current carbon footprint of concrete is not exactly very admirable.
(But it can be reduced! Read Ross Dimmock’s (Vice President, Tunnelling) excellent Normet blog: Steps towards creating zero-carbon tunnels
What we don’t often consider is that under almost every rock in the tunnel there are ways to cut down on material consumption. Having a smooth rock surface with minor overbreaks is one of these ways. There is simply less area to be sprayed, and the fundamentals of good application techniques like maintaining correct stand-off distance and angle between your nozzle tip and the surface, are far easier to maintain. Spraying becomes more systematic and layer thicknesses better stay under control. This inevitably leads to less concrete consumed for the same design structure, whether spraying to design layer thickness or to design profile.
Some of the other ways to control concrete consumption are more in the hands of the dedicated sprayed concrete people. Skilful and motivated operators with tight layer thickness control and good application technique, high-quality mix design and top-class equipment can ensure that waste is kept to a minimum.
Part of the work is already done before the tunnelling even begins. I recently read how a tunnel project had been able to reduce the quantity of sprayed concrete used by 20 per cent. This was achieved by using a high-performance concrete mix and being able to design thinner layers for permanent rock support.
Saving material on all fronts
So, long story short, I’d divide the areas where excess material consumption can be controlled, to five:
- Design: To be able to prescribe only the needed layer thicknesses and structures, nothing more.
- Excavation quality and profile control: To leave as little extra area to be sprayed as possible.
- Layer thickness control: To minimise over-spraying with good application technique and modern technologies helping the operator achieve the right layer thicknesses.
- Rebound: To get the precious grey stuff on the wall instead of the floor with sharp application techniques, equipment allowing low pulsation pumping and accurate accelerator dosing, and careful mix design.
- Waste and spill: To get the batching plant and delivery processes optimised so that no concrete goes to waste, and all of it goes to the nozzle.
As we see here, only two of these five areas are actually directly controlled by the sprayed concrete process. The rest are dependent on other processes of the tunnelling cycle, or even outside of it. Only being able to optimise all of these will lead to the best possible outcome considering the material consumption of the sprayed concrete process.
It’s a package deal!
So, it’s not enough to be able to look at individual sub-processes; it’s also key to understand the whole cycle and the dependencies between different parts. As well, it’s important to be aware of the stuff that is not directly on your own plate. If that driller would have gone for the shortest possible drilling time and hole count to save time, all the other processes in the cycle would have suffered.
For us at Normet, this means we cannot focus on individual products and processes and work in silos to optimise them. Maintaining a comprehensive understanding on all underground production processes and combining that with excellence in developing solutions for our customers is key. This optimises the whole excavation cycle for a more sustainable underground tomorrow. Additionally, this is why we target hiring people with industry experience in mining and tunnelling and share this underground expertise throughout the organisation to stay ahead of the game.
By the way, if you are a sprayer operator, get that driller a nice hot cup of coffee on the next morning shift. It will pay off!
About the author
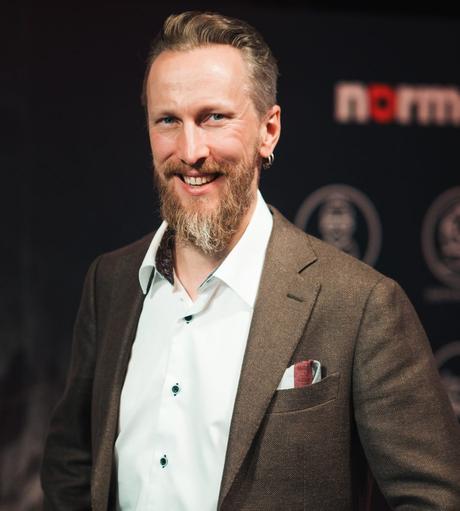
Panu Oikkonen
Director of Underground Process Excellence at Normet Group
Bio
Panu Oikkonen has been working for the underground tunnelling and mining industries for some 17 years. He has gained his on-site experience in hard rock drill & blast tunnelling projects, in positions ranging from assistant blaster to site management. Panu has a M.Sc. (Technology) degree in Rock Engineering. At Normet, Panu is developing know-how and technologies to improve underground processes. Panu is also the acting President in the Finnish Tunnelling Association FTA.
Panu Oikkonen - LinkedIn Profile